What is 5S and why is it so important?
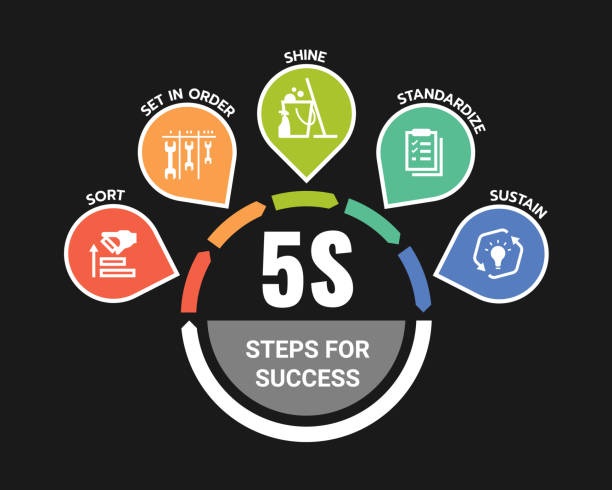
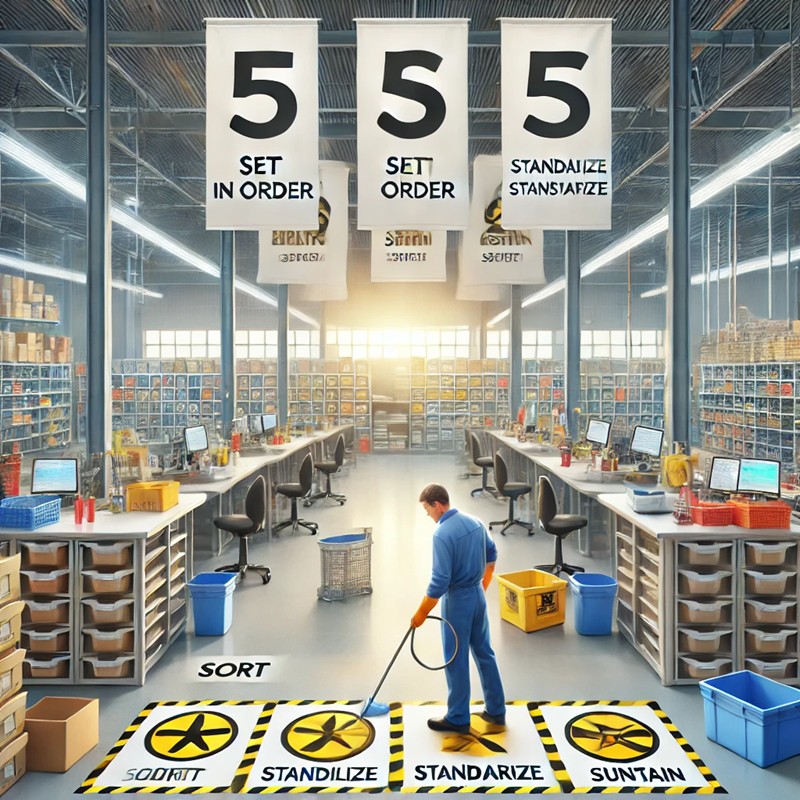
What is 5S?
5S is a workplace organization methodology originating from Japan, aimed at improving efficiency, productivity, and safety. The term "5S" comes from the initials of five Japanese words that describe its key principles:
- Seiri 整理(Sort)
Separate necessary items from unnecessary ones and dispose of what is not needed. - Seiton 整頓(Set in Order)
Organize necessary items so they are easy to find and access. - Seiso清掃 (Shine)
Keep the workplace clean and tidy to maintain a high standard of cleanliness. - Seiketsu清潔 (Standardize)
Establish standards to sustain the practices of sorting, organizing, and cleaning. - Shitsuke躾 (Sustain)
Develop discipline to follow the rules and maintain the 5S activities consistently.
Why is 5S so important?
5S is much more than just tidying up; it has a profound impact on workplace efficiency, safety, and overall performance. Here are the key reasons why 5S is essential:
1. Improves Safety
- A well-organized and clutter-free workspace reduces the risk of accidents and injuries, such as tripping or falling.
- Regular cleaning helps identify equipment issues early, preventing major breakdowns or hazardous situations.
2. Boosts Productivity
- When everything is organized, workers spend less time searching for tools or materials, enabling them to focus on their tasks.
- A clutter-free environment facilitates smoother workflows and reduces unnecessary movements.
3. Enhances Quality
- Clean and organized workplaces minimize the risk of contamination or defects, especially in industries like food production or precision manufacturing.
- A well-maintained environment reduces human errors, ensuring consistent quality in production.
4. Reduces Costs
- Removing unnecessary items saves storage and management costs.
- Preventive maintenance through regular cleaning extends equipment lifespan and minimizes repair expenses.
5. Improves Employee Morale
- A clean, organized workplace creates a positive and motivating work environment.
- Employees develop a sense of pride and ownership in their workplace, fostering a culture of responsibility and teamwork.
Conclusion
5S is a powerful tool for creating a safe, efficient, and productive work environment. By implementing and sustaining 5S, organizations can achieve long-term benefits, including higher quality, lower costs, and greater employee satisfaction.